제품 카테고리
- C 케이블 및 어댑터를 입력하십시오 40
- USB5 케이블 9
- USB 나사 잠금 케이블 26
- 커넥터 및 케이블 18
- 맞춤형 배선 하네스 33
- 허브 47
- 전자 스위치 공급 업체 5
- USB 앵글 케이블 27
- 터미널 안테나 9
- 의료용 케이블 37
- USB4 케이블 11
- POGO 핀 케이블 10
- 방수 케이블 28
제품 태그
Functional Production of Wiring Harnesses for Medical Devices
Functional production of wiring harnesses for medical devices involves a precise, quality-controlled process that blends automation and manual assembly. It includes cutting, 스트리핑, crimping, and terminating wires, followed by routing, bundling, and testing for electrical functionality and durability, with special attention to sterilization-ready designs and biocompatible materials.
As the core connection component of medical devices, the design and application of medical equipment harnesses cover the following key areas:
나. Definition and Function
Definition: Medical equipment harnesses are integrated electrical connection systems consisting of wires, insulation layers, connectors and protective covers. They are mainly used for power, signal and data transmission inside the equipment.
Core Function: Including signal transmission, power supply and equipment safety assurance to ensure the efficient and coordinated operation of medical instruments.
![]() Custom medical device electrical wiring harnesses, cable assemblies |
![]() Medical Device Cables – ISO 13485 and ISO 9001 Certified Manufacturer |
![]() CT medical equipment wiring-DB25P-DP37PIN multi-pin terminal assembly |
Design and Prototyping: The process begins with a team of engineers designing the harness to meet specific medical device requirements. This includes creating a design prototype that is then tested for quality and durability.
Cutting and Stripping: Wires are cut to precise lengths and the insulation is stripped using automated machinery, ensuring accurate wire dimensions.
Crimping or Soldering: Terminals are crimped or soldered to the exposed wire ends for reliable electrical connections.
Assembly and Routing: Wires are routed through sleeves, secured with ties, and connected to terminals according to the design. The harness is then bundled and may be protected with sleeves or heat-shrink tubing.
Testing and Inspection: Thorough electrical testing is conducted to verify continuity, insulation resistance, and overall functionality. Physical inspection for proper routing and damage is also performed.
Quality Control and Certification: Rigorous quality control protocols are followed to ensure adherence to medical industry standards like ISO 13485. Biocompatibility of materials is also a critical consideration, especially for sterilization-ready designs.
Customization and Packaging: Harnesses are often customized for specific medical applications and packaged for easy integration into devices or hospital systems.
II. Application Areas
Diagnostic Equipment
Electrocardiographs (ECGs) transmit electrode signals through harnesses;
Ultrasonic scanners rely on harnesses to achieve image transmission between probes and hosts.
Therapeutic Equipment
Hemodialysis machines monitor vital sign parameters through harnesses;
Laser surgical equipment uses harnesses to precisely control energy output.
Monitoring and Portable Equipment
Critical care monitors transmit patient vital sign data in real time;
Wearable devices use lightweight harnesses to support chronic disease monitoring.
III. Materials and technical requirements
Material selection: High temperature resistant and corrosion resistant materials (such as fluoroplastics) 선호됩니다, and some manufacturers introduce environmentally friendly and degradable materials;
Design standards: Electrical performance (such as conductive stability), 기계적 강도 (bending resistance) and medical-grade safety certification (such as ISO 13485) must be met;
Manufacturing process: It involves steps such as wire twisting, insulation injection molding, precision welding, and some scenarios require customized processing (such as endoscope harnesses).
IV. Composition structure
Components | 기능 | Material examples |
Wires | Transmit current/signal | Tinned copper wire, fluoroplastic wire |
Insulation | Prevent short circuit/leakage | PVC, PE, fluoroplastic |
커넥터 | Achieve modular docking | GH1.5 series, M12 plug |
Protective sleeves | Anti-interference and mechanical protection | Metal shielding layer, medical corrugated tube |
다섯. Typical manufacturers
Kanghong Medical: Focuses on surgical instrument cables (high-frequency electrosurgical cable, blood oxygen cable, 등.), and has passed ISO 13485 certification;
Yongrui Electronics: Provides customized services for complete sets of wire harnesses and connectors for medical equipment;
Shengpai Cable: Supply ROHS-certified medical-grade fluoroplastic harnesses.
VI. 지침
Avoid replacing special models with ordinary harnesses to prevent equipment compatibility issues;
Regular maintenance inspections, especially connector wear in high-frequency use scenarios;
Supplier qualifications and product certification documents must be verified when purchasing.
Key Considerations for Medical Wiring Harnesses:
Reliability and Durability:
Medical devices operate in demanding environments, requiring harnesses to be durable and withstand repeated use and sterilization.
Biocompatibility:
Materials used in medical harnesses must be biocompatible to avoid any adverse reactions or contamination.
Sterilization Compatibility:
Harnesses must be designed to withstand various sterilization methods, such as autoclaving, chemical cleaning, and UV exposure.
Regulatory Compliance:
Manufacturers must adhere to relevant regulations and standards, including ISO 13485.
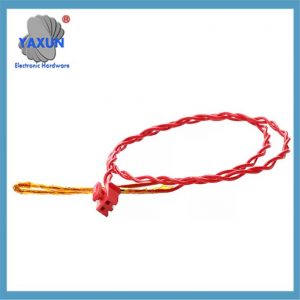
Medical equipment ct imaging cable manufacturers
문의하기
이메일을 기다리는 중, 이내에 답변해 드리겠습니다. 12 필요한 귀중한 정보를 몇 시간 동안.