I/O output harness design specifications and precautions for control signals
1. Wiring specifications and signal isolation
Independent wiring principle: I/O output lines must be laid separately from input lines and analog signal lines to avoid sharing cables or the same path to reduce electromagnetic interference.
Output type distinction:
Independent output: Different groups can support different voltage types (such as DC 24V, AC 220V).
Common output (COM terminal): The same group of outputs must use the same voltage type and polarity to avoid mixing and causing short circuits or equipment damage.
Photoelectric isolation: All I/O interfaces must use photoelectric isolation technology to isolate industrial field circuits from internal control circuits and improve anti-interference capabilities.
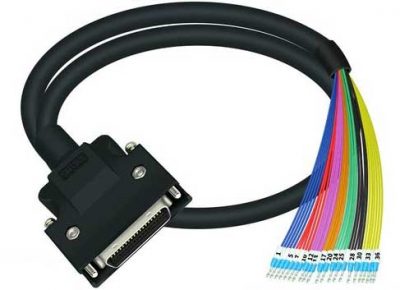
SCSI36-TB CN type 36-core servo drive relay data cable adapter cable harness 0.5m
Signal Transmission: I/O output harnesses transmit control signals from a controller (like a PLC) to devices like sensors, actuators, and motors.
Data Transfer: They can also facilitate the transmission of data between different systems, such as between a computer and a robotic arm.
Power Distribution: In some cases, these harnesses also provide power to connected devices.
Types and Features:
I/O Modules:
These are specialized modules that can convert various I/O signals (e.g., digital, analog) into a format suitable for transmission.
Harness Construction:
I/O output harnesses are designed with robust connectors, shielding to prevent interference, and durable materials to withstand harsh conditions.
Customization:
They can be customized with different connector types, cable lengths, and shielding options to suit specific application needs.
Applications:
Industrial Automation:
Used for controlling motors, valves, and other machinery in manufacturing and industrial processes.
Robotics:
Used for controlling robot arm movements, sensor inputs, and other robot functions.
Transportation:
Used for controlling traffic signals, railway systems, and other transportation infrastructure.
Building Automation:
Used for controlling lighting, Systémy HVAC, and other building systems.
2. Power and load management
External power supply introduction: If an external 24V power supply is used, ensure that the COM terminal is consistent with the polarity of the external power supply (positive or negative) to avoid reverse connection.
Load type adaptation:
Relay output: Suitable for inductive loads (such as motors and solenoid valves), and a freewheeling diode or a RC absorption circuit needs to be added to suppress the reverse electromotive force.
Transistor/thyristor output: Suitable for high-frequency switching loads, and attention should be paid to the maximum current limit (such as 50mA) and short-circuit protection.
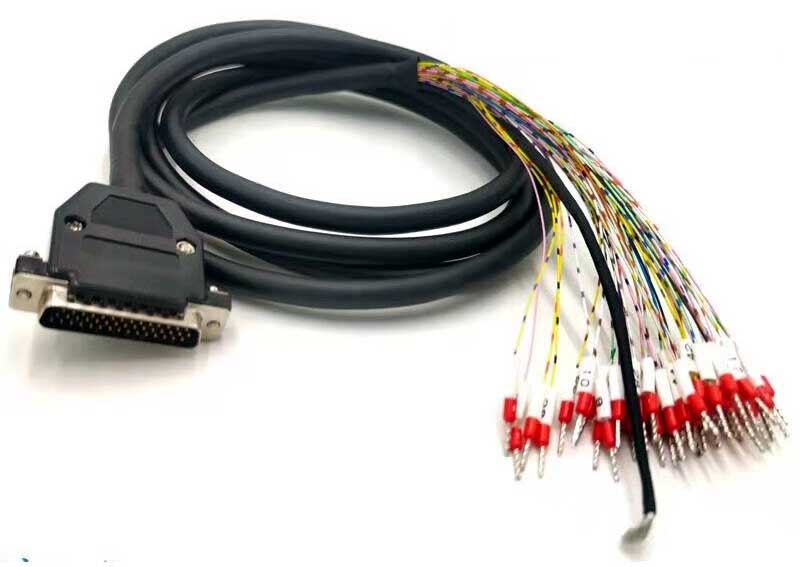
Servo drive 44-pin IO control CN1 and PLC signal control cable 0.5m
3. Anti-interference and filtering measures
Shielded cable: Analog signal transmission requires the use of twisted shielded cables, and at least one end of the shielding layer is grounded (the grounding resistance must be less than 1/10 of the shielding layer resistance).
RC filtering: The input end can be configured with an R-C filter (time constant 10~20ms) to reduce the interference of high-frequency noise on the output signal.
4. Safety protection design
Overcurrent protection: A short circuit in the output load may burn the PCB, and a fuse or current limiting circuit needs to be installed.
Anti-reverse connection design: For NPN/PNP sensors or external devices, it is necessary to confirm that the signal polarity matches to avoid reverse current causing port damage.
5. Typical application scenarios
Servo drive output: The digital output (DO) needs to be connected to a freewheeling diode to prevent high-voltage pulses when the relay is disconnected.
PLC control cabinet: The output module (such as CJ1W-OC211) supports 16-point relay output, which is suitable for start-stop control of industrial equipment.
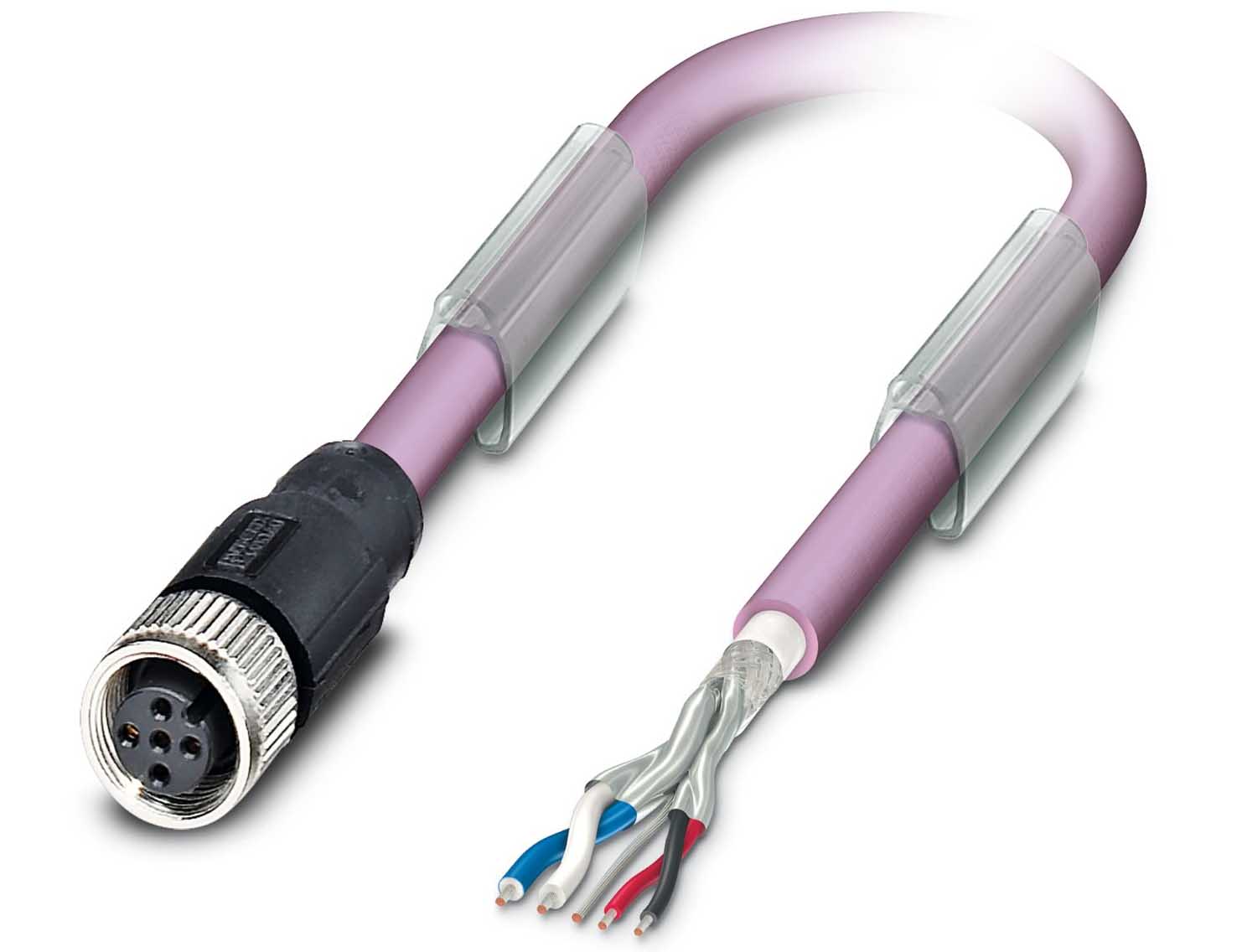
I/O Output shield Harnesses for Control Signals transfer data
Summary
The design of the I/O output harness needs to comprehensively consider signal isolation, load matching, anti-interference and safety protection. In actual applications, it is necessary to strictly follow the wiring specifications of the equipment manual and select the appropriate protection circuit for different load types to ensure long-term stable operation of the system.
AC servo motor driver refers to a controller that drives AC servo motors. It can receive feedback signals from encoders, senzory, atd., and control the speed and position of the servo motor according to the control instructions to achieve precise motion control.
Panasonic motor servo cable; Siemens motor servo; Mitsubishi Motor servo; Delta motor servo; Yaskawa motor servo; Omron motor servo; Sanyo Electric servo wiring harness; Hechuan servo connecting cable; Sankyo servo connecting cable; Keyence motor servo wiring harness.
The main features and advantages of AC servo motor drives include:
1. High precision: Using advanced servo control technology, it can achieve high-precision positioning and speed adjustment through precise control.
2. High reliability: It has high reliability and stability, and can adapt to harsh working environments and harsh working conditions.
3. Multiple control modes: Supports multiple control modes, such as position control, speed control, force control, atd., to achieve a variety of motion control needs.
4. Self-protection function: It has a self-protection function that can automatically identify abnormal situations and perform corresponding protection to avoid damage to the equipment due to abnormal operations.
5. Easy to debug: It is simple and easy to debug, which can improve the motion control accuracy and stability of the equipment.
6. Rich communication interfaces: Supports a variety of communication interfaces, such as CAN bus, RS485, atd., making the connection with the control system more convenient.
AC servo motor drives are widely used in automated control systems, such as automated processing equipment, printing equipment, robots, packaging equipment, textile equipment, pharmaceutical equipment and other fields. Able to achieve high-precision, high-speed, and high-reliability motion control.
AC servo motor driver wiring harness features
1. Contains Multiple Individual Wires: A wire harness is an electrical assembly that contains multiple individual wires that are grouped and bundled.
2. Neat organization: Wire harnesses are generally braided, braided or sleeved to make the circuits neatly organized for easy installation. During use, it can effectively avoid kinking and entanglement between lines.
3. Save space: The wire harness can accommodate a large number of wires and cables in a limited space, saving space and conforming to the compact and efficient design concept.
4. Easy to repair and replace: Branch power and control lines in the wiring harness can be easily replaced or repaired without shutting down the entire system.
5. Strong durability: The wires and cables built into the wiring harness are regularly measured and tested to ensure their quality and durability, thereby ensuring their long-term use in harsh environments.
6. Safe and reliable: The wiring harness is manufactured using standard materials and processes, with reliable quality and safe use. When following correct maintenance methods and usage specifications, wire harnesses have the advantages of long life, high performance, safety and reliability.