Kluczowe punkty zarządzania jakością dla montażu wiązki przewodów
I. Kontrola kluczowych elementów procesu
Przetwarzanie podstawowe zawodowe
Powierzchnia rdzenia drucianego musi być sprawdzona pod kątem Burrs, Obrażenia i inne wady. Gdy długość przekracza 50 metry, Konieczne jest wiercenie otworów na środku i użycie specjalnej maszyny do usuwania drutu do przetwarzania.
Długość usuwania i dokładność zaciskania terminalu bezpośrednio wpływają na wyniki przewodzące, A zakres tolerancji musi być ściśle kontrolowany.
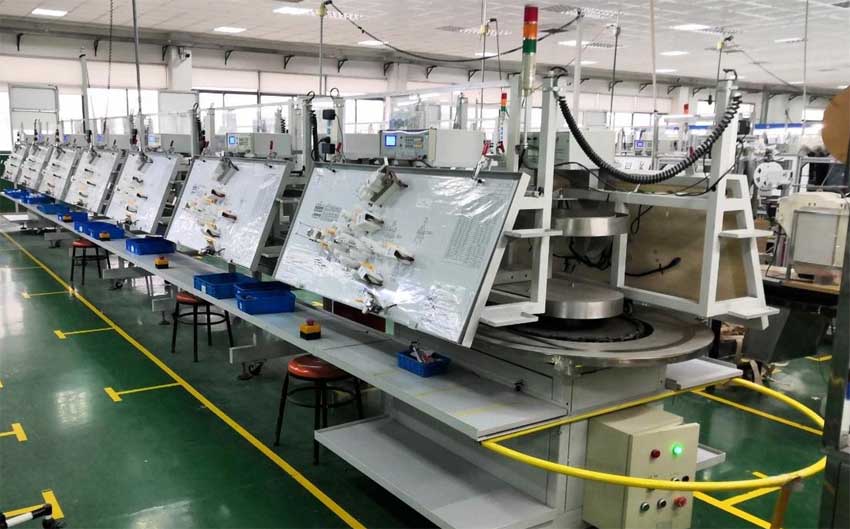
Linia montażu wiązki przewodów dla reflektorów samochodowych
Proces łączenia
Napraw rdzeń drutu zgodnie z wymaganiami dotyczącymi kierunku i długości wiązki przewodów, aby upewnić się, że układ tablicy narzędzi spełnia specyfikacje projektowe i uniknąć skrzyżowania lub uwikłania.
Punkty rozgałęzienia wiązki przewodów muszą być chronione taśmą lub rękawami, aby zapobiec zużyciu i zakłóceniu elektromagnetycznym.
Wybór materiałów
Zewnętrzna powłoka powierzchniowa jest najlepiej wykonana z izolacji plastiku (Wysoka wytrzymałość mechaniczna i odporność na korozję chemiczną), a materiały gumowe lub metalowe mogą być używane w specjalnych scenariuszach.
Kluczowe aspekty zarządzania jakością wiązki przewodów:
Inspekcja materiałów przychodzących:
Ostrożnie sprawdzanie przychodzących przewodów, złącza, i inne elementy wad, takie jak uszkodzona izolacja, Niepoprawne rozmiary, lub korozja przed montażem.
Kontrola procesu montażu:
Wykorzystanie zautomatyzowanego sprzętu i narzędzi, takie jak zaawansowane maszyny do cięcia i usuwania, Aby zapewnić dokładne i spójne przygotowanie drutu.
Etykietowanie i identyfikacja:
Wdrożenie czystego i niezawodnego systemu znakowania dla przewodów i komponentów, aby zapobiec zamieszaniu podczas montażu, konserwacja, i rozwiązywanie problemów.
Kontrole i testowanie w trakcie procesu:
Przeprowadzenie regularnych kontroli jakości w całym procesie montażu, w tym testy pierwszej armii, Kontrole zaciskane, i testy elektryczne.
Routing i wiązanie:
Zapewnienie odpowiedniego routingu i pakietu w celu zapobiegania punktom naprężeń, ostre zakręty, i potencjalne problemy z przegrzaniem.
Testowanie końcowe:
Przeprowadzanie dokładnych testów elektrycznych i fizycznych na gotowej wiązce przewodów, aby upewnić się, że spełnia wymagania dotyczące wydajności i standardy branżowe.
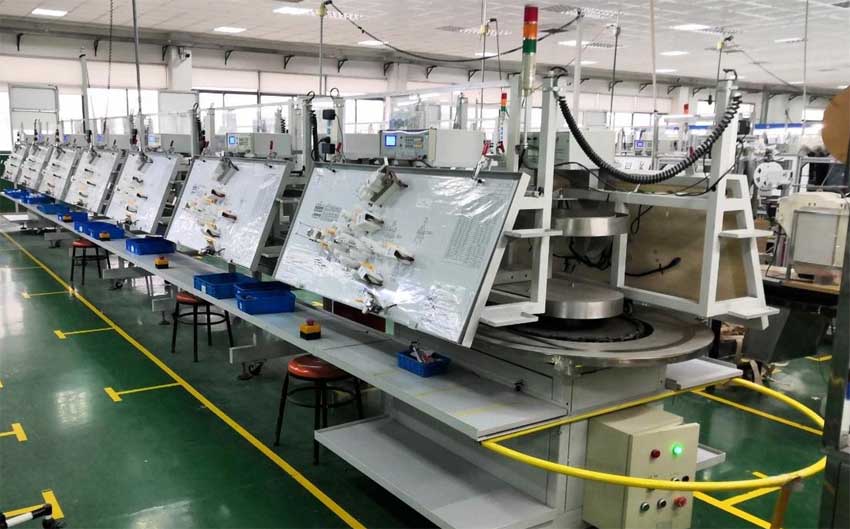
Linia montażu wiązki przewodów dla reflektorów samochodowych
Ii. Środki kontroli jakości Test kondycjonowania i izolacji
Integralność połączenia obwodu jest weryfikowana za pomocą testu ciągłości, i test rezystancji izolacji musi spełniać standard ≥100 mΩ.
Wiązania przewodów wysokiego napięcia wymagają dodatkowych testów napięcia wytrzymałego (takie jak 1500 V/1 min bez awarii).
Kontrola i inspekcja wielkości
Sprawdź wizualnie status zaciskania terminalu, Taśma owijanie jednolitość i klarowność etykiet .
Użyj zacisku, aby zmierzyć długość wiązki, Kąt gałęzi i inne parametry, aby upewnić się, że spełniają wymagania rysunku.
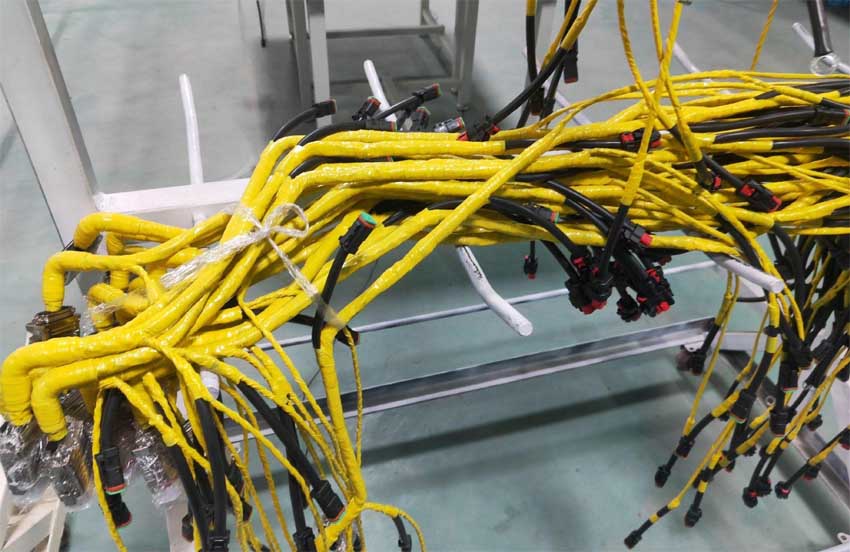
Pojazdy energetyczne, Maszyna budowlana, magazynowanie energii, Zasilanie linii montażowej wiązki wiązki wiązki wiązki
3. Zarządzanie parametrami procesu
Crimping and Salding Control
Nacisk zacisku końcowego musi zostać dostosowany zgodnie z średnicą drutu, a błąd wysokości zaciskania jest kontrolowany w ciągu ± 0,1 mm.
Spawanie ultradźwiękowe musi monitorować amplitudę, Parametry ciśnienia i czasu, aby uniknąć spawania zimnego lub nadmiernego uzyskiwania.
Optymalizacja procesu powlekania
Temperatura ogrzewania i czas rurki kurczącej ciepła wymagają dopasowania do właściwości materiału, aby zapobiec nierównomiernemu skurczowi lub deformacji.
Podczas pakowania wielu pasm wiązek przewodów, Odstępy między więziami kablowymi powinny być przechowywane, a wartość napięcia powinna być ustawiona na 10-15N.
4. Środowisko produkcyjne i specyfikacje personelu
Warsztaty muszą utrzymać stałą temperaturę i wilgotność (Zalecane 25 ℃ ± 2 ℃, wilgotność ≤60%) w celu zmniejszenia ryzyka deformacji materiału.
Operatorzy muszą być regularnie szkolone, koncentrując się na wzmocnieniu pomiarów przeciwstatycznych i znormalizowanych procedur operacyjnych.
Poprzez wyżej wymienione środki kontrolne, Szybkość wydajności zespołu wiązki przewodów można systematycznie ulepszyć, a stabilność układu elektrycznego pojazdu można zapewnić.
Z powodów pracy, Często komunikuję się z menedżerem jakości wiązki przewodów, A najczęstsze skargi, które słyszę: praca jest trudna do wykonania, Personel jest trudny do zarządzania, A jakość jest trudna do kontrolowania. Zewnętrznie są skargi od klientów, Wewnętrznie istnieją różne naciski na pojemność produkcyjną i sprzęt, kłopoty wewnętrzne i zewnętrzne, a menedżerowie jakości są często bardzo zajęci.
Kluczem do rozwiązania problemu „zajętej” jakości wiązki przewodów jest „zapobieganie”. Skargi od klientów zewnętrznych często wynikają ze złej wewnętrznej kontroli jakości. Aby osiągnąć dobrą jakość, Musimy zapobiegać problemom na miejscu, NIP Problemy w zarodku, I złap je w zarodku.
Jak „zapobiegać”?
W trakcie przetwarzania przeprowadzane są trzy inspekcje: Pierwsza inspekcja, Kontrola patrolu i kontrola końcowa.
Charakterystyka wstępnego przetwarzania: Wysoki stopień automatyzacji, kluczowe pozycje, stosunkowo stabilna jakość, Ale gdy wystąpią problemy, może wystąpić produkcja partii, a wartość RPN jest wysoka. Oprócz regularnych kontroli TPM sprzętu każdego dnia roboczego, Pracownicy muszą również przeprowadzić „trzy inspekcje” podczas procesu produkcyjnego.
W terminalu operacji zaciskania, przednie i tylne wymiary wysokości i szerokości oraz wartość siły ciągnącej są kluczowymi elementami sterującymi. Odpowiednie wartości muszą być zarejestrowane dla pierwszej i ostatniej kontroli i kontroli patrolowych każdej zmiany. Pierwsza inspekcja, kontrola przed rozpoczęciem zmiany. Masową produkcję można przeprowadzić dopiero po zakwalifikowaniu pierwszego kawałka zaciśnięcia. W przeciwnym razie, Sprzęt musi być debugowany, dopóki nie zostanie zakwalifikowany. Kontrola jest niezbędną częścią. Kontrola jest zwykle przeprowadzana przez inspektorów z działu QC. Celem kontroli jest zapewnienie stabilności terminalu i zmniejszenie ryzyka jakości. Kontrola końcowa jest łatwo przeoczonym linkiem. Pracownicy często są zajęci opuszczeniem pracy lub przełączaniem materiałów, zaniedbanie ostatecznej inspekcji. Celem Inspekcji Ostatnich elementów jest zmiana i zapisanie liczby partii zaciśniętej w celu ułatwienia przyszłej identyfikowalności partii.
Rób trzy rzeczy dobrze w procesie przetwarzania końcowego: Nie akceptuj, Nie wytwarzać, i nie przekazuj wadliwych wiązek przewodów
Charakterystyka końcowa: wiele procesów, wielu pracowników, niski stopień automatyzacji, Typowe pracochłonne operacje. Zarządzanie jakością procesów końcowych koncentruje się na kultywowaniu świadomości jakości pracowników. Poprzez ciągłe szkolenie i uczenie się zasad jakości „trzech nie”, Pracownicy wiedzą, co robić i jak to zrobić.
Niedopuszczalne: Wszelkie wadliwe produkty nie będą akceptowane, takie jak niewłaściwa średnica drutu końcowego znaleziona na stacji podpasowej, Niewłaściwe wyciekające otwory znalezione na stacji montażowej, Niespójne wymiary znalezione na stacji kontroli wyglądu, itp. Wszystkie te wymagają świadomości wzajemnej inspekcji;
Nie wyprodukowane: Proces działania nie powoduje wad. Dokumenty takie jak instrukcje pracy, kluczowe pozycje, a zabezpieczenie błędów musi być wyraźnie widoczne, a pracownicy muszą ściśle przestrzegać instrukcji. Kontrola „push-pull-push” terminali wtyczkowych na stacji podzesple jest typowym przykładem, co jest nierozerwalnie związane ze świadomością pracowników na temat samokontroli;
Nie przechodząc: Po odkryciu wady, Użyj biurokracji, aby wyraźnie oznaczyć podejrzaną lokalizację, izolować to, i nie przekazuj go do następnego procesu. To jest szczególna świadomość pracowników.
Zarządzanie jakością wiązek przewodów na miejscu nie jest zadaniem jednego działu lub jednej osoby. Wymaga to od całego zespołu współpracy w celu ciągłego poprawy i robienia 3+3 na miejscu, aby zrobić duży krok do przodu w jakości.