Phân tích chi phí khai thác dây ô tô
TÔI. Cấu trúc chi phí
Chi phí vật liệu (kế toán cho 76%-80%)
dây điện: Vật liệu cốt lõi là đồng, và chi phí chiếm khoảng 38%-86%25. Biến động giá đồng ảnh hưởng trực tiếp đến tổng chi phí (Giá đồng hiện tại là về 65,000 RMB/tấn, Giá nhôm là 18,000 RMB/tấn, và chi phí của dây nhôm chỉ là 1/4 của dây đồng). Connector: Chứa vỏ nhựa (Vật liệu PA66/PBT) và thiết bị đầu cuối kim loại, và chi phí đúc phun của vỏ nối không thấm nước là về 0.8 RMB/mảnh. Vật liệu khác: vỏ bọc, phần cuối, niêm phong, vân vân., Mua sắm chiếm khoảng 18%-29%. Chi phí lao động (kế toán cho 13%-20%)
70% quy trình sản xuất cần được hoàn thành thủ công, bao gồm cả lắp ráp, Kiểm tra và các liên kết khác, và tỷ lệ chi phí lao động tăng lên theo sự phức tạp của quá trình. Chi phí nguyên liệu thô:
Đồng, nhôm, và các hợp chất nhựa là vật liệu thiết yếu, và giá của chúng dao động, tác động đến chi phí chung.
Chi phí sản xuất:
Chúng bao gồm lao động sản xuất, máy móc, và sự phức tạp của thiết kế khai thác, có thể ảnh hưởng đáng kể đến thời gian sản xuất và chi phí.
Chi phí khác:
Điều này bao gồm chi phí hành chính, Hỗ trợ phát triển, và chi phí vận chuyển.
Chi phí lao động:
Lắp ráp thủ công, đặc biệt là cho các dây nịt phức tạp, có thể tốn nhiều công sức và tốn kém, Đóng góp vào tổng chi phí, Theo một cuộc thảo luận về Quora.
Chi phí quản lý độ phức tạp:
Các biến thể trong thiết kế khai thác và sự phức tạp của việc quản lý các biến thể đó có thể thêm vào chi phí phát triển và sản xuất, Theo một whitepaper của Siemens.
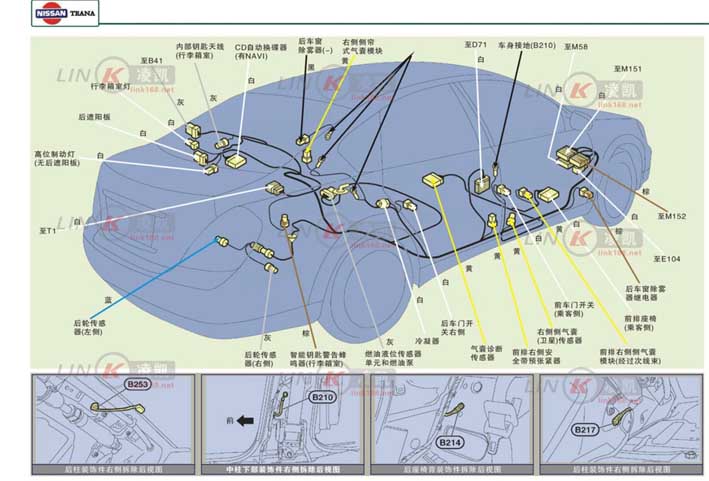
Phân tích chi phí khai thác hệ thống dây ô tô
Chi phí khác
Chi phí sản xuất, R&D Chia sẻ, Giao thông vận tải và kho, chi phí chất lượng, và lợi nhuận thuế chiếm khoảng 7%-10%.
Ii. Các yếu tố ảnh hưởng chính
Thay thế dây đồng bằng dây nhôm có thể giảm chi phí vật liệu bằng cách 75%, Nhưng nó là cần thiết để cân bằng tính dẫn điện và rủi ro an toàn.
Công nghệ hệ thống dây điện FPC (Độ dày 0,8-1.2mm) có thể giảm độ dày của dây nối và quá trình lắp ráp, và giảm chi phí lao động.
Sự phức tạp của quá trình
Số lượng nhánh dây nối và chiều dài của dây (Yêu cầu ký quỹ dành riêng) ảnh hưởng trực tiếp đến lượng đồng được sử dụng. Ví dụ, Khai thác dây chính của một mô hình nhất định cần 4,5kg dây đồng không có oxy, và các tài khoản đồng cho 38% của tổng chi phí.
Chi phí của dây có đường kính dây khác nhau thay đổi đáng kể (Ví dụ, Đơn giá của dây 0,35mm² là 42% thấp hơn 1,5mm²).
Maintion và chi phí thay thế
Phạm vi chi phí của sự thay thế dây nối hộp số lớn là lớn: Về 800-1000 Yuan (không bao gồm giờ lao động) Đối với các cửa hàng sửa chữa thông thường, và 4s mua các bộ phận ban đầu + Giờ lao động có thể đạt đến 2400 Yuan.
Iii. Hướng tối ưu hóa chi phí công nghiệp
Đổi mới công nghệ: Áp dụng thiết kế mạch tích hợp hệ thống dây điện FPC để giảm hệ thống dây điện phức tạp của dây dẫn truyền thống. 1.
Sức mạnh tổng hợp và giảm chi phí: Sử dụng dây nhôm trong các thành phần không quan trọng và hợp kim nhôm cường độ cao cho các bộ phận cấu trúc để đạt được không gian giảm trọng lượng lớn hơn.
Nâng cấp AAUTOMATION: Cải thiện tốc độ tự động hóa của các quy trình mở và uốn để giảm sự phụ thuộc thủ công.
Iv. Các trường hợp điển hình: Khai thác hệ thống dây điện áp thấp có giá trị hơn 5,000 Yuan trên mỗi chiếc xe, vượt xa các mô hình thông thường (2,000-5,000 Yuan).
Xiaomi tranh cãi tự động: Giải pháp dây đồng thay thế dây nhôm tiết kiệm 3,480 Yuan mỗi mô hình, Nhưng đặt ra câu hỏi về hiệu quả và an toàn giảm cân.
(Ghi chú: Dữ liệu chi phí trên dựa trên các điều kiện thị trường và thông tin công khai trong 2025.)
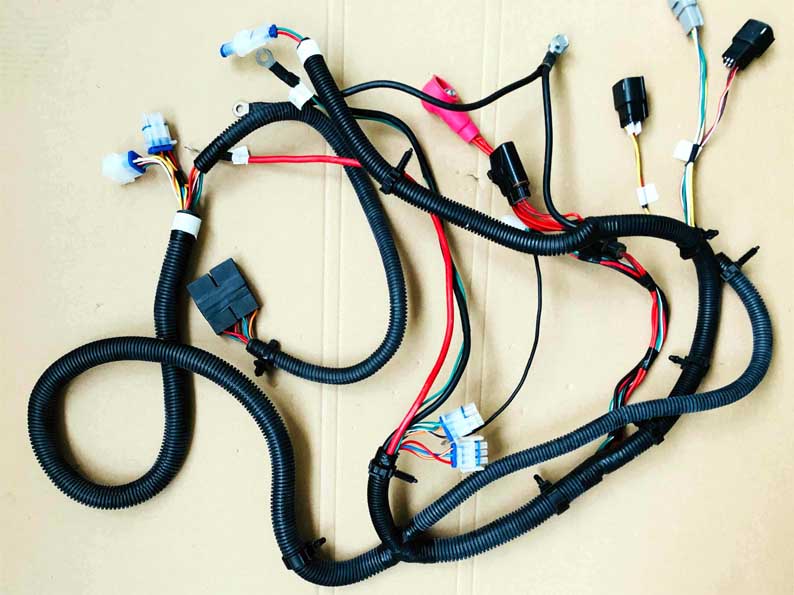
Nhà sản xuất và nhà cung cấp dây truyền động ô tô Trung Quốc
Xu hướng thị trường và cân nhắc:
Tăng trưởng thị trường toàn cầu:
Thị trường khai thác hệ thống dây ô tô đang có sự tăng trưởng nhất quán, Được thúc đẩy bởi việc tăng sản xuất xe và nhu cầu về các tính năng nâng cao.
Sự thống trị khu vực:
Châu Á-Thái Bình Dương, đặc biệt là Trung Quốc, Thống trị thị trường do cơ sở sản xuất ô tô mạnh mẽ và chi phí lao động thấp hơn.
Tác động của xe điện:
Sự gia tăng của xe điện (EVS) đang tạo ra những cơ hội mới để khai thác dây, nhưng cũng giới thiệu những thách thức mới, chẳng hạn như nhu cầu về các hệ thống điện áp cao hơn và các yêu cầu vật liệu khác nhau, Theo báo cáo của Imarc Group.
Tự động hóa trong sản xuất:
Tự động hóa việc khai thác dây đang ngày càng trở nên quan trọng để giảm chi phí, Cải thiện hiệu quả, và giải quyết sự phức tạp ngày càng tăng của các phương tiện hiện đại.
Tóm lại, Chi phí khai thác hệ thống dây điện là một sự tương tác phức tạp của chi phí vật liệu, Chi phí sản xuất, nhân công, và các yếu tố khác. Thị trường toàn cầu đang phát triển, với sự thống trị châu Á-Thái Bình Dương, Và sự gia tăng của EV đang tạo ra những cơ hội và thách thức mới cho ngành công nghiệp.
Từ bài viết trước đây, nói về tỷ lệ vật liệu khai thác dây, chúng tôi đã học được rằng chi phí của vật liệu khai thác dây điện cho khoảng 65% của tổng chi phí của dây nịt. Trong giai đoạn thiết kế, Chi phí khai thác dây có thể được giảm chủ yếu bằng cách tối ưu hóa thiết kế dây nịt. Trong giai đoạn sau, Chi phí khai thác dây sẽ được giảm chủ yếu bằng cách tối ưu hóa quá trình sản xuất của các nhà cung cấp dây nịt và so sánh giá cả.
Các nghiên cứu đã chỉ ra rằng 80% chi phí sản phẩm được xác định trong giai đoạn thiết kế. Vì thế, Nhiều công ty đã đầu tư rất nhiều năng lượng để chú ý đến việc này 80% Thiết lập chi phí, và đang khám phá các phương pháp giảm chi phí hơn nữa trước r&D Sản phẩm nhập sản xuất hàng loạt. Vì thế, Nó có ý nghĩa rất lớn khi tiến hành nghiên cứu và ứng dụng giảm chi phí trong giai đoạn thiết kế dây dẫn động ô tô và tối ưu hóa hơn nữa chi phí khai thác dây.
Chi tiết kỹ sư dây nịt dây: Nền tảng và thiết kế tiêu chuẩn hóa, Tối ưu hóa kiến trúc và tích hợp bộ điều khiển, Tối ưu hóa bố cục dây nịt, Đổi mới công nghệ khai thác dây, Vật liệu một-nhiều và bản địa hóa. Cũng như Vave từ 6 Phương pháp giảm chi phí trong giai đoạn thiết kế dây nịt. Và áp dụng trong các dự án phát triển xe, Hiệu ứng giảm chi phí là đáng kể.
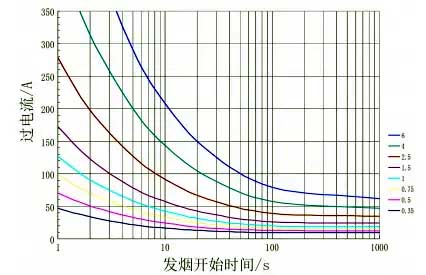
Tối ưu hóa chi phí của dây điện áp điện áp thấp ô tô
Nền tảng và thiết kế tiêu chuẩn hóa
Để giảm chi phí sản phẩm và rút ngắn chu kỳ phát triển, Thiết kế nền tảng đã trở thành một trong những biện pháp giảm chi phí quan trọng cho các công ty ô tô. Thông qua kết nối dây nịt, Giao diện khai thác dây và nền tảng định nghĩa vị trí lỗ của các thiết bị điện có thể được quảng bá. Liên tục thúc đẩy nền tảng của các vật liệu khai thác dây và các giải pháp thiết kế, thống nhất các thành phần khai thác dây và đơn giản hóa cấu trúc, trong đó cải thiện tiêu chuẩn hóa thiết kế và giảm tính độc đoán của thiết kế kỹ sư. Các mô hình khác nhau nên chia sẻ các thành phần thứ cấp của dây nối càng nhiều càng tốt. Thiết lập một cơ sở dữ liệu về các thành phần khai thác dây và cố gắng sử dụng các thành phần nền tảng hiện có để tránh phát triển các thành phần mới đặc biệt. Việc thống nhất các thành phần khai thác dây có thể tập trung nhu cầu, có lợi cho việc mua sắm các thành phần và tăng chip thương lượng. Sau khi thiết kế tối ưu hóa nền tảng liên tục, Tỷ lệ phổ biến của hộp điện cabin phía trước, Bảng điều khiển hộp điện, Các kết nối dây nối và các phụ kiện khai thác dây đã đạt được 100%. Về mặt các bộ phận và đầu nối, Có tổng cộng 312 Các loại bộ phận và thành phần, 208 trong đó dựa trên nền tảng, và tỷ lệ dựa trên nền tảng tăng lên 67%.
Trước khi tối ưu hóa, Có tổng cộng 5 Các loại hộp điện PFB, bao gồm 4 các loại lát gạch và 1 Loại gắn bên. Sau khi tối ưu hóa, Chỉ có 3 loại. Sau đây là trường hợp tối ưu hóa thiết kế nền tảng của Hộp điện PFB cho một dự án nền tảng nhất định. Ba loại hộp điện PFB được hợp nhất và tối ưu hóa thành một loại như trong hình 3.
Tối ưu hóa kiến trúc và tích hợp bộ điều khiển
Tối ưu hóa liên tục của kiến trúc ô tô không chỉ có thể cải thiện hiệu suất của ô tô, nhưng cũng giảm chi phí sản xuất. Thúc đẩy tối ưu hóa kiến trúc điện có thể đơn giản hóa hiệu quả cấu trúc khai thác dây. Số lượng thành phần điện càng lớn, Khai thác càng dài. Thúc đẩy sự tích hợp của các thiết bị điện có thể làm giảm số lượng đầu nối và các nhánh khai thác dây. Lấy một dự án xe điện làm ví dụ, Kiến trúc điện điện áp cao đã được tối ưu hóa, và chi phí và chất lượng của dây điện có điện áp cao đã giảm đáng kể. Sau khi kiến trúc ô tô được tối ưu hóa, Độ dài của dây nịt điện điện áp cao được giảm từ 22 m to 9 m, khối lượng được giảm từ 13.5 kg đến 4.8 kg, và chi phí của dây nịt điện điện áp cao giảm đáng kể 41%, Như thể hiện trong hình 4 Và 5.
Tối ưu hóa bố cục dây nịt
Do việc áp dụng một số lượng lớn các bộ phận điện và không gian nối dây nhỏ trong xe, Khó khăn trong bố cục dây nịt tiếp tục tăng. Trong thiết kế và bố cục của dây nối ô tô, dây nịt phải an toàn và ổn định, Lưu vật liệu, Tiết kiệm không gian, và dễ dàng lắp ráp và duy trì. Cải thiện hơn nữa tính đồng nhất của bố cục thiết bị điện, Giảm các loại vật liệu cố định, và giảm và đơn giản hóa việc sử dụng các bảng bảo vệ. Tránh các nguồn nhiệt và giảm áp dụng các vật liệu cách nhiệt có thể tối ưu hóa hướng khai thác và bố cục. Tối ưu hóa bố cục của các thành phần điện có thể rút ngắn và đơn giản hóa đường dẫn dây điện. Hình 6 Và 7 Hiển thị trước và sau khi tối ưu hóa bố cục dây nối cho một dự án nhất định. Vị trí bố cục của các thành phần vẫn không thay đổi, và cơ thể được quay 180 °. Đầu nối giao diện ăng -ten được thay đổi từ hai đầu nối 2pin thành bốn đầu nối 1pin, trong đó ba đầu nối 1pin được kết nối trực tiếp với thành phần A, và cái khác được kết nối với dây nịt. Khai thác dây được giảm bởi 3 Vật liệu dây nhỏ cho 3 vòng lặp ăng -ten được kết nối với thành phần A, Độ dài khoảng 1m, và bộ nạp dây nối được rút ngắn. Tổng chi phí giảm cho tối ưu hóa bố cục này xấp xỉ $4.6.
Sự đổi mới trong công nghệ khai thác hệ thống dây điện
Bằng cách giới thiệu các công nghệ mới trong Vật liệu khai thác dây, Thiết kế và quy trình, Khai thác dây có thể nhẹ và giảm chi phí. Ví dụ, bằng cách áp dụng công nghệ thu nhỏ rơle và cầu chì, Tổng chi phí của hộp điện được giảm khoảng 29.5 Yuan. Cho một ví dụ khác, Trong cùng điều kiện trở kháng, dây dẫn nhôm có khối lượng nhỏ hơn dây dẫn đồng (Xem bảng 1). Bằng cách chọn dây nhôm và dây có đường kính mịn có đường kính ngoài nhỏ hơn và trọng lượng nhẹ hơn, Trọng lượng và chi phí của dây nịt có dây ô tô có thể giảm. Chi phí dây điện chiếm một tỷ lệ lớn chi phí khai thác dây ô tô, Và 0.13 Dây hợp kim MM2 hoặc thậm chí các dây vuông nhỏ thấp hơn được thúc đẩy. Ứng dụng của 0.13 dây hợp kim MM2 có ý nghĩa lớn đối với toàn bộ xe. Trong một dự án nhất định, các 48 V dây nối pin được sử dụng 35 dây đồng mm2 trước khi tối ưu hóa, nhưng đã thay thế chúng bằng 50 dây nhôm mm2 sau khi tối ưu hóa. Độ dài là về 4 m, và trọng lượng được giảm 224 g/m. Giảm tổng trọng lượng của 896 G đã đạt được, và chi phí đã giảm khoảng 30 Yuan, như trong hình 8.
Vật chất một-nhiều và bản địa hóa
Giải pháp kỹ thuật trước đó tương ứng với một loại thứ hai- và vật liệu cấp ba, và đã được biến thành một mô hình một-nhiều của cùng một vật liệu, Cung cấp một thư viện tài nguyên lựa chọn của người Viking cho các nhà cung cấp cấp độ đầu tiên. Các nhà máy khai thác dây được tài trợ ở nước ngoài và các nhà máy khai thác dây địa phương chọn vật liệu chi phí thấp dựa trên hệ thống mua sắm của riêng họ để tăng cường sức mạnh thương lượng của các nhà cung cấp dây nịt và cải thiện sự ổn định của chuỗi cung ứng. Các giải pháp một-nhiều như thiết bị đầu cuối mặt đất, Nhiệt ống co lại, cầu chì, Ống và dây thông thường đã được triển khai. Lấy còng dựa trên vải của một dự án nhất định làm ví dụ, còng dựa trên vải có cùng đường kính có thể được chọn và hoán đổi giữa ba thương hiệu khác nhau, Như thể hiện trong bảng 2. Tăng tỷ lệ nội địa hóa của vật liệu thứ cấp và đại học và giảm chi phí vật liệu đã trở thành các biện pháp giảm chi phí chính cho nhiều bộ phận và thành phần. Khi mức độ thông minh của các kết nối trong nước tiếp tục tăng, Các nhà sản xuất kết nối trong nước tiếp tục đổi mới công nghệ, Và chất lượng của các đầu nối trong nước ngày càng tốt hơn. Bởi vì các đầu nối nhập khẩu thường đắt tiền và có chu kỳ giao hàng dài, Các thương hiệu kết nối trong nước đã nhận được nhiều sự chú ý hơn. Trong khi đảm bảo chất lượng, Các dây nối của nhiều dự án mô hình xe đang sử dụng các đầu nối trong nước để thay thế một số đầu nối thuộc sở hữu nước ngoài, giảm chi phí vật liệu khai thác dây và cải thiện sự ổn định của chuỗi cung ứng. Một số kết nối và phụ kiện trong một dự án đang được thay thế bởi các thương hiệu trong nước như Hulian và Aohai, Như thể hiện trong bảng 3.
VAVE giảm chi phí
Hiện tại, Các công ty ô tô ngày càng trở nên nhận thức hơn về việc giảm chi phí VAVE. Các hoạt động giảm chi phí vận động có thể giảm hiệu quả chi phí khai thác dây và cải thiện hiệu quả chi phí của các sản phẩm. Vì khó khăn hơn và tốn kém hơn để thực hiện VAVE sau khi sản xuất hàng loạt, Sự chú ý nhiều hơn hiện được trả cho việc áp dụng Vave trong giai đoạn thiết kế. Hiện tại, Cơ chế của các cuộc họp thường xuyên của nhóm dự án được sử dụng đầy đủ, Và tất cả các bộ phận liên quan đều tham gia đầy đủ vào các hoạt động VAVE. Hãy để các kỹ sư có liên quan trong mỗi bộ phận biết các biện pháp và nội dung cụ thể của kế hoạch VAVE, và tích cực hợp tác với việc quảng bá và thực hiện các đề xuất khai thác dây hiệu quả. Đề xuất và thực hiện VAVE khai thác dây cũng không thể tách rời với sự tham gia tích cực và hợp tác của các nhà cung cấp dây nịt dây. Bộ phận thiết kế dây nịt thường xuyên tổ chức các cuộc họp dự án thường xuyên với các nhà cung cấp khai thác dây để trao đổi các giải pháp VAVE và theo dõi tiến trình, Thúc đẩy hiệu quả việc thực hiện giải pháp VAVE.
Bộ phận Thiết kế khai thác dây đã phát triển một bảng ghi âm VAVE để đảm bảo rằng kế hoạch VAVE được phát triển thẳng thừng. Cho mỗi dự án, Danh sách Vavecheck của dự án được biên soạn dựa trên bảng ghi Vave. Các bản vẽ của mỗi van được xem xét theo danh sách kiểm tra VAVE. Có tổng cộng 12 Các loại loại tối ưu hóa trong bảng VAVE. Lấy một mô hình xe nhất định làm ví dụ, thông qua tối ưu hóa liên tục của Vave trong giai đoạn thiết kế, Chi phí của vật liệu khai thác hệ thống dây điện đã được giảm 11%. Lấy dây nịt hệ thống và dây nối của mô hình này làm ví dụ như một ví dụ, Giải pháp khai thác hệ thống dây điện ban đầu trước khi tối ưu hóa VAVE tách các dây nối trần ra khỏi dây nối của thân và kết nối chúng nội tuyến qua hai cặp dây nối để tạo thành hai dây nối độc lập. Quản lý riêng biệt và tập hợp các thành phần riêng biệt không phải là giải pháp thiết kế tối ưu từ quan điểm về chi phí và chất lượng. Trong các điều kiện bố cục hiện có, Sau khi phân tích VAVE và xem xét toàn diện tất cả các khía cạnh, Khai thác hệ thống dây trần có thể được tích hợp vào dây đai hệ thống cơ thể. Sau khi tích hợp các thành phần khai thác dây không dây, Bạn có thể quản lý một thành phần ít hơn và giảm chi phí công cụ. Sau khi sáp nhập dây trần dây nịt vào dây nịt sau khi VAVE, Không có dây đai dây trần như trong hình 9 và hình 10. Thông qua tối ưu hóa VAVE, chi phí được giảm bởi $3 và khối lượng được giảm 0. 1 kg/đơn vị. Sau khi công cụ được hợp nhất, Chi phí công cụ được giảm xấp xỉ $6,000.