電線線束組件的質量管理的關鍵點
我. 關鍵過程元素的控制
Wire核心處理
需要檢查電線芯的表面是否有毛刺, 損壞和其他缺陷. 當長度超過 50 儀表, 有必要在中間鑽孔並使用特殊的電線剝離機進行處理.
剝離長度和末端壓接的準確性直接影響導電性能, 而且公差範圍需要嚴格控制.
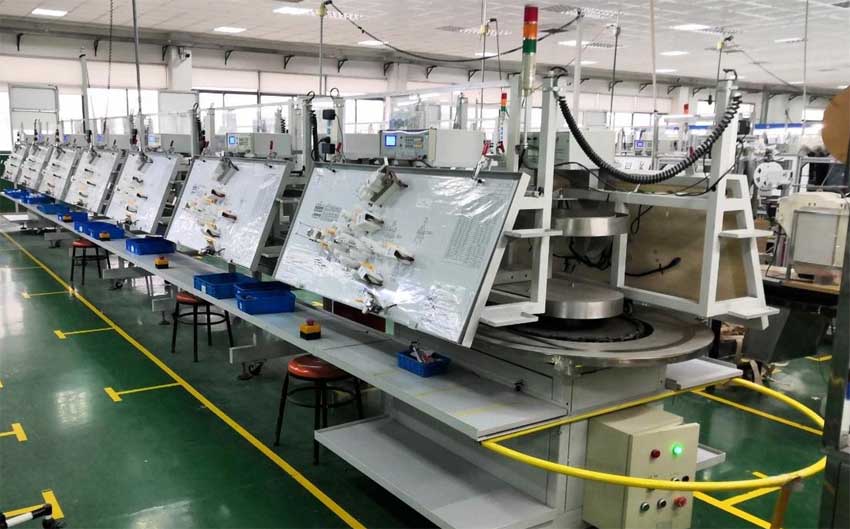
汽車大燈的接線線束裝配線
wwrewing Process
根據電線線束的方向和長度要求固定電線芯,以確保工具板的佈局符合設計規格並避免穿越或糾纏.
線束的分支點需要用膠帶或袖子保護,以防止磨損和電磁干擾.
塗料材料選擇
外表面塗層最好由絕緣塑料製成 (高機械強度和化學腐蝕性), 橡膠或金屬材料可用於特殊情況.
電線線束質量管理的關鍵方面:
傳入的材料檢查:
仔細檢查傳入的電線, 連接器, 以及其他缺陷等缺陷的組件, 大小不正確, 或組裝前的腐蝕.
組裝過程控制:
利用自動設備和工具, 例如高級切割和剝離機, 確保精確,一致的電線準備.
標籤和識別:
為電線和組件實施清晰穩固的標籤系統,以防止組裝過程中混淆, 維護, 和故障排除.
進程檢查和測試:
在整個組裝過程中進行定期質量檢查, 包括第一個學術測試, 壓接檢查, 和電測試.
路線和捆綁:
確保正確的電線路由和捆綁以防止壓力點, 尖銳的彎曲, 和潛在的過熱問題.
最終測試:
對成品線束進行徹底的電氣和物理測試,以確保其符合性能要求和行業標準.
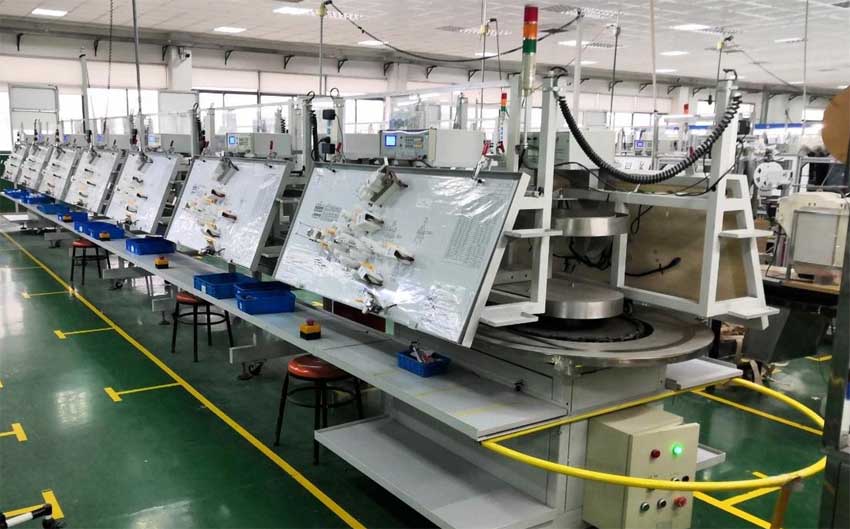
汽車大燈的接線線束裝配線
ii. 質量檢查措施導軌和絕緣測試
電路連接完整性通過連續性測試驗證, 絕緣電阻測試必須符合≥100MΩ的標準.
高壓線束需要額外的承受電壓測試 (例如1500V/1分鐘而沒有故障).
出現和尺寸檢查
視覺檢查終端壓接狀態, 膠帶包裹均勻性和標籤清晰度.
使用卡尺測量線束的長度, 分支角度和其他參數,以確保它們滿足圖紙的要求.
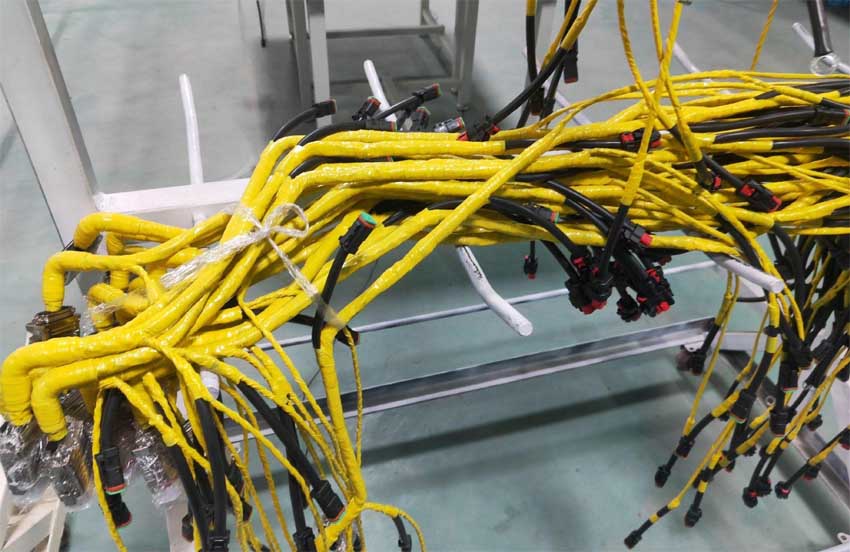
能源車, 施工機械, 儲能, 電池線束組件線
3. 過程參數管理
crimping和焊接控制
需要根據電線直徑調節末端壓力, 並且壓接高度誤差在±0.1mm之內受到控制.
超聲波焊接需要監測幅度, 壓力和時間參數以避免冷焊接或過度融化.
塗層過程優化
加熱溫度和熱收縮管的時間需要匹配材料特性,以防止收縮或變形不平坦.
當捆綁多個電線線束時, 電纜紮帶之間的間距應保持均勻, 張力值應設置為10-15n.
4. 生產環境和人員規格
研討會需要保持恆定的溫度和濕度 (推薦25±2℃, 濕度≤60%) 降低材料變形的風險.
操作員需要定期培訓, 重點是加強反靜態措施和標準化的操作程序.
通過上述控制措施, 線束組件的收益率可以系統地提高,並且可以確保車輛電氣系統的穩定性.
由於工作原因, 我經常與線束的質量經理進行交流, 我聽到的最常見的抱怨是: 工作很難做, 人員很難管理, 而且質量很難控制. 在外部有客戶的投訴, 在內部,生產能力和設備有各種壓力, 內部和外部麻煩, 質量經理通常非常忙.
解決電線線束“繁忙”質量問題的關鍵在於“預防”. 外部客戶的投訴通常是由於內部質量控制差而引起的. 取得良好的質量, 我們必須防止現場問題, 芽中的問題, 然後將它們咬在芽中.
如何“預防”?
在預處理中進行了三項檢查: 首次檢查, 巡邏檢查和最終檢查.
預處理的特徵: 高度自動化, 關鍵位置, 質量相對穩定, 但是一旦出現問題, 可能發生批處理, RPN值很高. 除了在每個工作日對設備進行定期檢查外, 員工還需要在生產過程中進行“三個檢查”.
在末端壓接運行中, 前後高度和寬度維度以及拉力值是關鍵控制項目. 必須記錄對每次班次的第一次也是最後一次檢查和巡邏檢查的相應值. 首次檢查, 開始班次之前檢查. 只有在第一塊壓接到資格之後才能進行批量生產. 否則, 設備需要調試,直到有資格. 檢查是必不可少的部分. 檢查通常由QC部門的檢查員進行. 檢查的目的是確保終端壓接的穩定性並降低質量風險. 最終檢查是一個容易被忽略的鏈接. 員工經常忙於下班或切換材料, 忽略最終檢查. 最終檢查的目的是更改和記錄犯罪批次的數量,以促進未來的批次可追溯性.
在後處理過程中做三件事: 不要接受, 不要生產, 並且不要傳遞有缺陷的電線線束
後處理特徵: 許多過程, 許多員工, 自動化程度低, 典型的勞動密集型操作. 後處理過程的質量管理著重於培養員工的質量意識. 通過持續培訓和學習“三個否”質量原則, 員工知道該怎麼做以及如何做.
不可接受: 任何有缺陷的產品都不會被接受, 例如在子組件站發現的錯誤的端子直徑, 在裝配站發現的錯誤洩漏孔, 在外觀檢查站發現的尺寸不一致, ETC. 這些都需要意識到相互檢查;
未製造: 操作過程不會產生缺陷. 諸如工作說明之類的文件, 關鍵位置, 必須清晰可見,防錯誤措施,並且員工必須嚴格遵循說明. 對子組裝站的插電終端檢查的“推力泵”檢查是一個典型的例子, 這與員工對自我檢查的認識是不可分之的;
沒有傳遞: 發現缺陷後, 使用繁文tape節清楚地標記可疑位置, 隔離它, 並且不要將其傳遞給下一個過程. 這是員工的特殊意識.
接線線束的現場質量管理不是一個部門或一個人的工作. 它要求整個團隊共同努力,以不斷改進和做 3+3 現場邁向質量邁出的一大步.