Key points of quality management for wire harness assembly
jeg. Control of key process elements
Wire core processing
The surface of the wire core needs to be checked for burrs, damage and other defects. When the length exceeds 50 meter, it is necessary to drill holes in the middle and use a special wire stripping machine for processing.
The stripping length and the accuracy of terminal crimping directly affect the conductive performance, and the tolerance range needs to be strictly controlled.
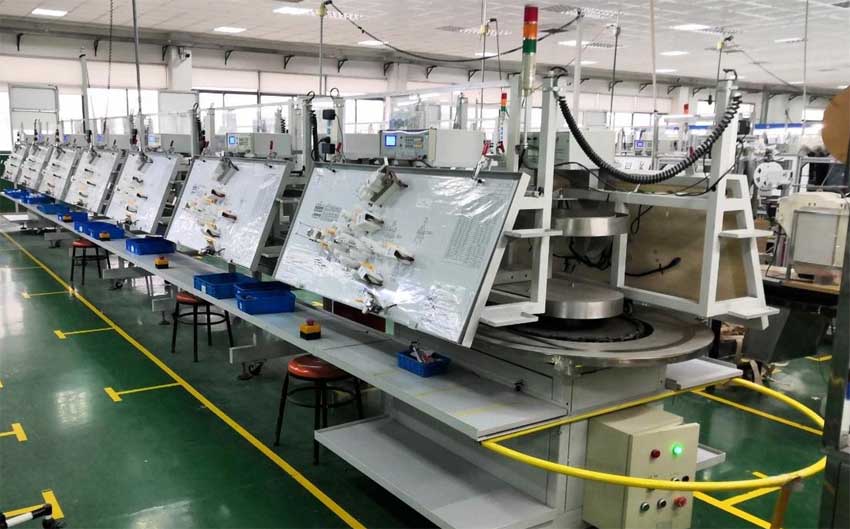
Ledningssele -samlebånd til bilforlygter
Wiring process
Fix the wire core according to the direction and length requirements of the wire harness to ensure that the layout of the tooling board meets the design specifications and avoid crossing or entanglement.
The branch points of the wire harness need to be protected with tape or sleeves to prevent wear and electromagnetic interference.
Coating material selection
The outer surface coating is preferably made of insulating plastic (high mechanical strength and chemical corrosion resistance), and rubber or metal materials can be used in special scenarios.
Key Aspects of Wire Harness Quality Management:
Incoming Material Inspection:
Carefully inspecting incoming wires, stik, and other components for defects like damaged insulation, incorrect sizes, or corrosion before assembly.
Assembly Process Control:
Utilizing automated equipment and tools, such as advanced cutting and stripping machines, to ensure accurate and consistent wire preparation.
Labeling and Identification:
Implementing a clear and robust labeling system for wires and components to prevent confusion during assembly, maintenance, and troubleshooting.
In-Process Inspections and Testing:
Conducting regular quality checks throughout the assembly process, including first-article testing, crimp inspections, and electrical testing.
Routing and Bundling:
Ensuring proper wire routing and bundling to prevent stress points, sharp bends, and potential overheating issues.
Final Testing:
Performing thorough electrical and physical tests on the finished wire harness to ensure it meets performance requirements and industry standards.
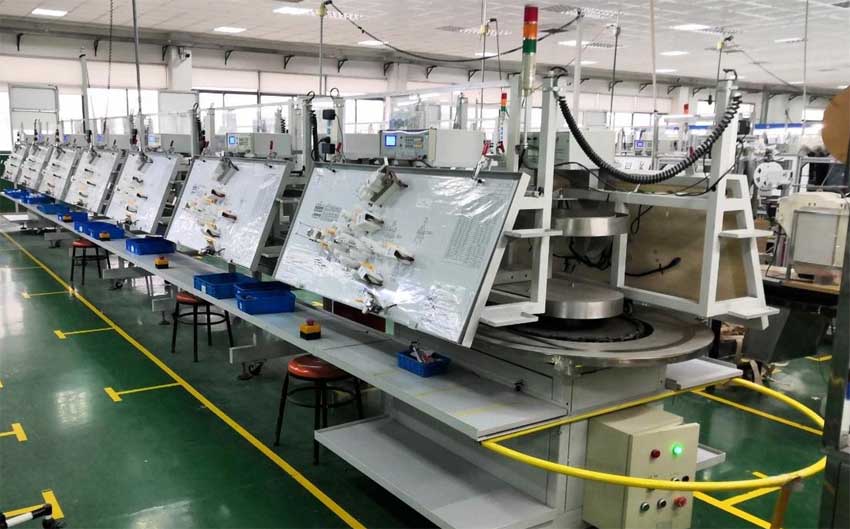
Ledningssele -samlebånd til bilforlygter
Ii. Quality inspection measures Conduction and insulation test
The circuit connection integrity is verified through the continuity test, and the insulation resistance test must meet the ≥100MΩ standard.
High-voltage wire harnesses require additional withstand voltage testing (such as 1500V/1min without breakdown).
Appearance and size inspection
Visually check the terminal crimping status, tape wrapping uniformity and label clarity.
Use a caliper to measure the length of the harness, branch angle and other parameters to ensure that they meet the requirements of the drawing.
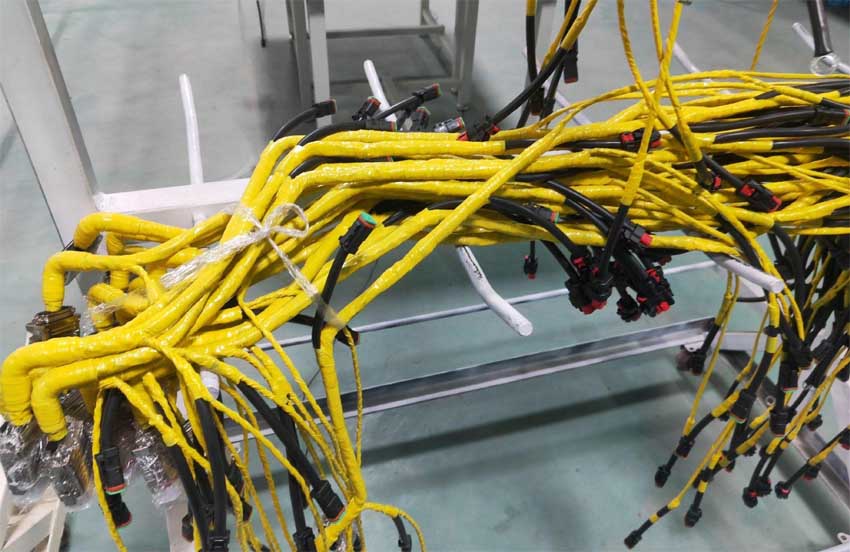
Energy vehicles, construction machinery, energy storage, power battery wiring harness assembly line
3. Process parameter management
Crimping and welding control
The terminal crimping pressure needs to be adjusted according to the wire diameter, and the crimping height error is controlled within ±0.1mm.
Ultrasonic welding needs to monitor the amplitude, pressure and time parameters to avoid cold welding or over-melting.
Coating process optimization
The heating temperature and time of the heat shrink tubing need to match the material properties to prevent uneven shrinkage or deformation.
When bundling multiple strands of wire harnesses, the spacing between the cable ties should be kept uniform, and the tension value should be set to 10-15N.
4. Production environment and personnel specifications
The workshop needs to maintain a constant temperature and humidity (recommended 25℃±2℃, humidity ≤60%) to reduce the risk of material deformation.
Operators need to be trained regularly, with a focus on strengthening anti-static measures and standardized operating procedures.
Through the above-mentioned control measures, the yield rate of wiring harness assembly can be systematically improved and the stability of the vehicle’s electrical system can be ensured.
Due to work reasons, I often communicate with the quality manager of the wiring harness, and the most common complaints I hear are: the work is difficult to do, the personnel are difficult to manage, and the quality is difficult to control. Externally there are complaints from customers, internally there are various pressures on production capacity and equipment, internal and external troubles, and quality managers are often extremely busy.
The key to solving the problem of “busy” quality of wire harness lies in “prevention”. Complaints from external customers often stem from poor internal quality control. To achieve good quality, we must prevent on-site problems, nip problems in the bud, and nip them in the bud.
How to “prevent”?
Three inspections are carried out in the pre-process: first inspection, patrol inspection and final inspection.
Characteristics of the pre-process: high degree of automation, key positions, relatively stable quality, but once problems occur, batch production may occur, and the RPN value is high. In addition to regular TPM inspections of equipment every working day, employees also need to do “three inspections” during the production process.
In the terminal crimping operation, the front and rear height and width dimensions and the pulling force value are the key control items. The corresponding values must be recorded for the first and last inspections and patrol inspections of each shift. First inspection, inspection before starting the shift. Mass production can only be carried out after the first piece of crimping is qualified. Ellers, the equipment needs to be debugged until it is qualified. Inspection is an indispensable part. Inspection is usually carried out by inspectors from the QC department. The purpose of inspection is to ensure the stability of terminal crimping and reduce quality risks. Final inspection is an easily overlooked link. Employees are often busy leaving get off work or switching materials, neglecting the final inspection. The purpose of final piece inspection is to change and record the number of crimping batches to facilitate future batch traceability.
Do three things well in the post-processing process: do not accept, do not manufacture, and do not pass on defective wire harnesses
Post-process characteristics: many processes, many employees, low degree of automation, typical labor-intensive operations. The quality management of post-process processes focuses on cultivating employees’ quality awareness. Through continuous training and learning of the “three no’s” principles of quality, employees know what to do and how to do it.
Not Acceptable: Any defective products will not be accepted, such as the wrong terminal wire diameter found at the sub-assembly station, wrong leaking holes found at the assembly station, inconsistent dimensions found at the appearance inspection station, etc. These all require awareness of mutual inspection;
Not manufactured: The operation process does not produce defects. Documents such as work instructions, key positions, and error-proofing must be clearly visible and employees must strictly follow the instructions. The “push-pull-push” inspection of plug-in terminals at the subassembly station is a typical example, which is inseparable from employees’ awareness of self-inspection;
Not passing on: After a defect is discovered, use red tape to clearly mark the suspicious location, isolate it, and do not pass it on to the next process. This is the special awareness of employees.
On-site quality management of wiring harnesses is not the job of one department or one person. It requires the entire team to work together to continuously improve and do 3+3 on-site to take a big step forward in quality.