Comprehensive Guide to Harness Connector Selection
أنا. Core Parameter Selection
Material and Structure
Prefer high temperature resistant (≥125℃) and corrosion resistant materials such as polyamide and polyurethane to ensure long-term stable connection1.
For high voltage harnesses, attention should be paid to the conductor material (such as copper core) and cross-sectional area. For high temperature environments (such as above 180℃), a larger cross-sectional area wire should be selected.
Electrical Performance
Match the terminal width and current carrying capacity (such as 0.64mm terminal carrying 10A, 7.8mm terminal carrying 60A) according to the load characteristics (steady-state/transient current, voltage waveform).
For low voltage scenarios, select 12V/24V connectors. For high voltage applications (such as new energy vehicles), select products with a rated voltage of more than 600V and a shielding layer. Current Rating: Ensure the connector can handle the maximum current flowing through the circuit without overheating or damage.
Voltage Rating: The connector’s insulation and contact materials must withstand the maximum voltage applied.
Number of Circuits/Contacts: Determine the number of wires (circuits) you need to connect and select a connector with sufficient contact positions.
Wire Gauge: The size of the wires (AWG) will influence the type of contacts and the overall connector size needed.
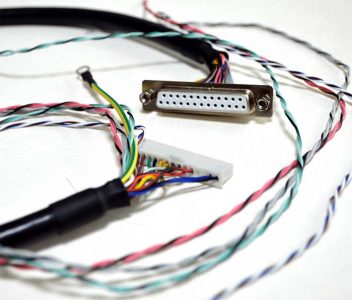
خط طرف الأسلاك المخصص DB
Interface and size adaptation
Select the connector size according to the harness diameter to avoid poor contact or loose crimping.
Match the interface type (round/square, plug/socket) with the compatibility of the receiving end to ensure a reliable physical connection.
Crimp vs. Solder: Crimp contacts are often preferred for field repairability, while solder contacts can offer better sealing against moisture.
الثاني. Mechanical and protective properties
Mechanical life and plug-in force
The plug-in and pull-out times requirements (such as ≥50 times) must be met, and the terminal and sheath matching force must be stable to avoid accidental separation.
In high-voltage or vibration scenarios, connectors with locking structures (such as secondary locks) are preferred.
Environmental protection level
IP67/IP69K waterproof grade products must be selected for humid or dusty environments, and medical equipment harnesses must withstand frequent disinfection.
Extreme temperature (-40℃~125℃) applications require verification of material weather resistance.
Temperature Range: Select connectors that can withstand the expected operating temperatures.
Sealing and IP Rating: Consider the need for sealing against moisture, dust, or other contaminants.
Vibration and Shock: If the harness will be subjected to vibration or shock, choose connectors designed to withstand these forces.
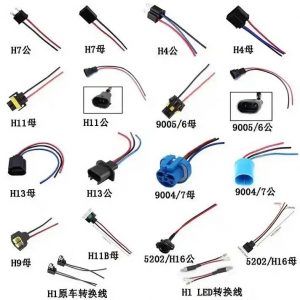
Select connectors. Terminal wire processing China manufacturing factory
ثالثا. Application scenario adaptation New energy vehicle high voltage system Requires the use of high voltage cables with shielding layers, optimizes the path layout to reduce vibration friction, and selects insulation materials with a withstand voltage of ≥400V.
Medical/industrial equipment The blood oxygen harness of the monitor must be compatible with the probe type (such as adult/child soft finger sleeves) and brand interfaces (such as Mindray, GE).
رابعا. Brand service and maintenance Prefer TE, Aptiv and other brands to obtain original technical support and certification data. Regularly check the oxidation and corrosion of the terminals, and clean the dust/grease to maintain performance.
Summary: The selection needs to be comprehensive in terms of materials, electrical parameters, mechanical properties and usage scenarios, combined with brand services and maintenance costs, and priority should be given to obtaining certified products through formal channels.
Space Constraints: Consider the available space for the connector and ensure it fits within the design.
Engagement Force: Think about how easy the connector should be to connect and disconnect, especially in difficult-to-reach areas.
Mating Type: Choose between male (plug) and female (socket/jack) connectors based on your application.
Ⅴ. Other Considerations:
Certifications and Approvals: If your application requires specific certifications (e.g., أول, CSA), ensure the connector meets those standards.
Cost: Compare different connector types and brands to find the right balance between performance and budget.
Availability and Lead Times: Ensure the connector is readily available and has a reasonable lead time.
By carefully considering these factors, you can select a connector that provides a reliable and durable connection for your wiring harness application.
The connector is the core component of the wiring harness. The performance of the connector directly determines the overall performance of the wiring harness, and plays a decisive role in the electrical stability and safety of the entire vehicle.
To connect the wiring harness connector on the equipment side, just select the connector that matches it. Despite this, as wiring harness engineers, we should be more professional in connector selection than other component engineers. The selection of connectors at the equipment end follows the following principles:
Consider factors such as the plug-in’s usage environment, درجة حرارة, dry and wet zones, vibration, إلخ. to ensure design reliability.
The manufacturers of male and female connectors must have the same requirements, and the matching of the connectors must be ensured.
Manufacturers of male and female terminals have consistent plating requirements to ensure good contact with electrical devices, minimize contact resistance, and improve reliability. There are no special requirements, generally tin plating is used.
For terminal connectors used in airbags and other applications that require higher performance, gold-plated parts should be given priority to ensure safety and reliability.
If the same kind of sheath is used in the same wire harness, its color must be different, and it is best to use physical error proofing.
Based on the overall coordination of the car’s appearance, black or dark-colored sheathing should be preferred in the engine compartment.
When the connector requires via holes, the outer dimensions of the sheath should be able to meet the sheet metal via holes. Normally, the ratio of the sheet metal hole diameter to the minimum installation width of the sheath should be above 1.5:1.
On the premise of improving connection reliability, consider miniaturization, lightweight and product price.

Select waterproof connector terminals for automotive connector harnesses