Key points for selecting and installing air conditioning connection cables
1. Cable types and specifications
Material requirements
Pure copper core cables must be used to ensure conductivity and corrosion resistance, such as RV-type multi-strand copper core soft wires or flat hard sheathed wires.
High-power air conditioners such as cabinet units require cables with a wire diameter of 4 square meters or more, and ordinary wall-mounted units can choose 2.5 square meters.
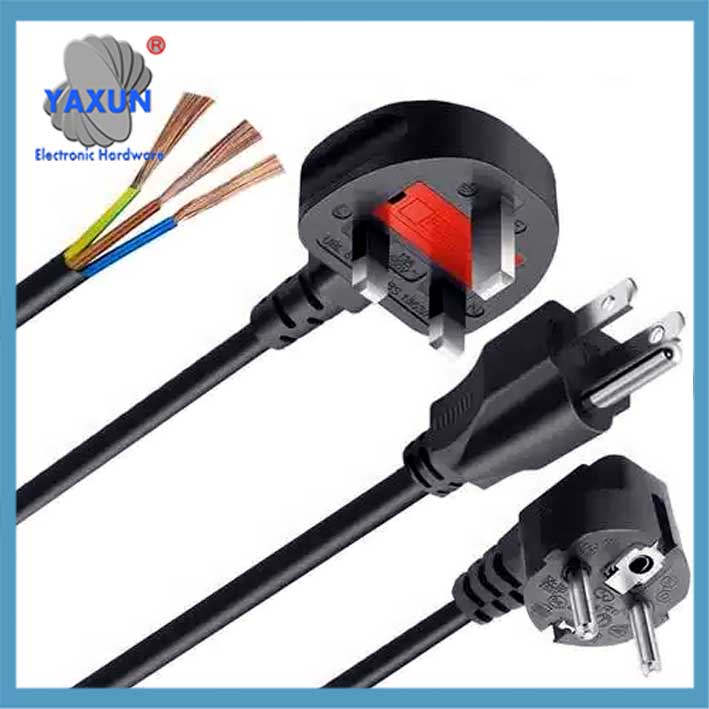
European standard, American standard air conditioner Appliance power cord
Core number configuration
The connection between the internal and external units of split air conditioners must include power cables and signal cables, and the common configuration is four-core (4×1 square) or five-core (4 square×2+1.5 square×3).
2. Installation specifications
Wiring standards
Strong and weak wire pipes must be kept at a distance of more than 30 cm to avoid signal interference; power lines and signal lines should be laid in separate casings.
Refrigerant pipes, drain pipes and cables must be fixed separately, and the drain pipe must reserve a 1% inclination and install a lifting elbow.
Wiring requirements
Follow the principle of “left zero, right phase (live), top ground”, connect the live wire to the switch, and the neutral wire to the lamp holder.
The wiring terminal needs to be wrapped with insulating tape to ensure that there is no exposure; it is recommended to use splash-proof type for cabinet power socket.
III. Purchase suggestions
Certification and guarantee: Give priority to products that meet national standards (such as marked “national standard four-core wire”), and pay attention to whether the merchant provides material guarantee, buyer guarantee and other services.
Scenario adaptation: Select the wire diameter according to the air conditioner power, Zum Beispiel, 4 square wire is suitable for cabinets above 3 horsepower, Und 1.5-2.5 square wire is suitable for wall-mounted machines.
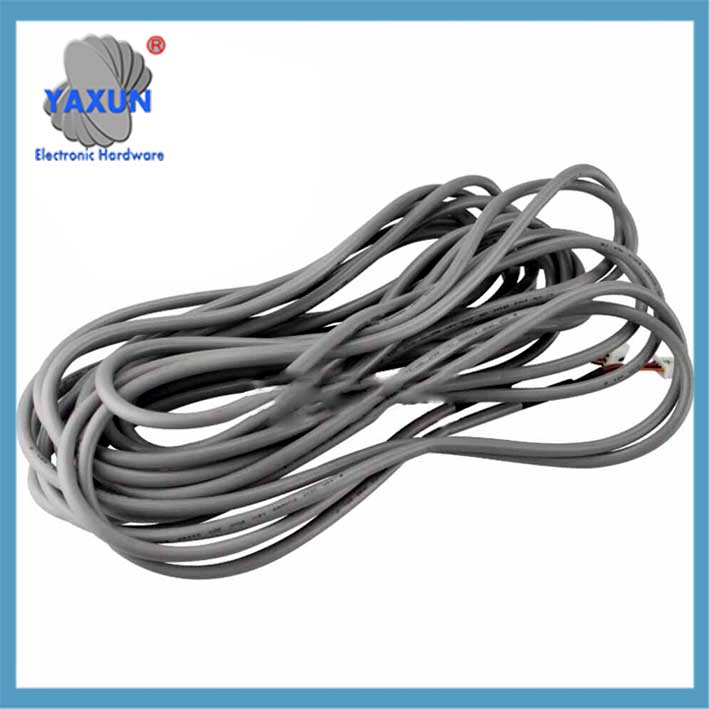
Custom Gree Air Conditioner Duct Machine Connection Cable 4pin Signal Cable 8M
IV. Precautions
When extending the cable, the standardized wiring method must be adopted. It is forbidden to extend the cable at will to cause poor contact or safety hazards.
After the water and electricity construction is completed, it is necessary to test the insulation and check the tightness of all joints to avoid circuit breakage or leakage during operation.
The stability and safety of the air conditioning system can be guaranteed through the above standardized selection and installation.
When we consider the cost-reduction design of wire harnesses, we require the use of as few wire harness connectors as possible. Jedoch, I believe everyone has encountered this situation recently. More and more OEMs have separated the air conditioning wiring harness on HVAC from the instrument wiring harness. Now the question comes, is it necessary to split?
We know that if the air conditioning wiring harness is separated separately, the cost of the wiring harness will inevitably increase. A pair of connectors are added to connect the air conditioning wiring harness and instrument wiring harness.
Gleichzeitig, the splitting of the air conditioning wiring harness will bring the following benefits:
1. The air-conditioning wiring harness is supplied together with the HVAC, which can shorten the assembly time of the main engine factory.
2. Convenient assembly
3. Contribute to the modular design of wiring harnesses
But beyond that, are there any other considerations?
Wire Harness Engineer Scatter saw an article recently. The point of view is probably that if the air-conditioning wire harness is not segmented, the instrument wire harness will come down from the relatively stationary instrument pipe beam and be assembled to the HVAC (there will be vibration when the HVAC is working). The constant vibration of the wiring harness caused fretting corrosion of the terminals, which eventually triggered a car recall.
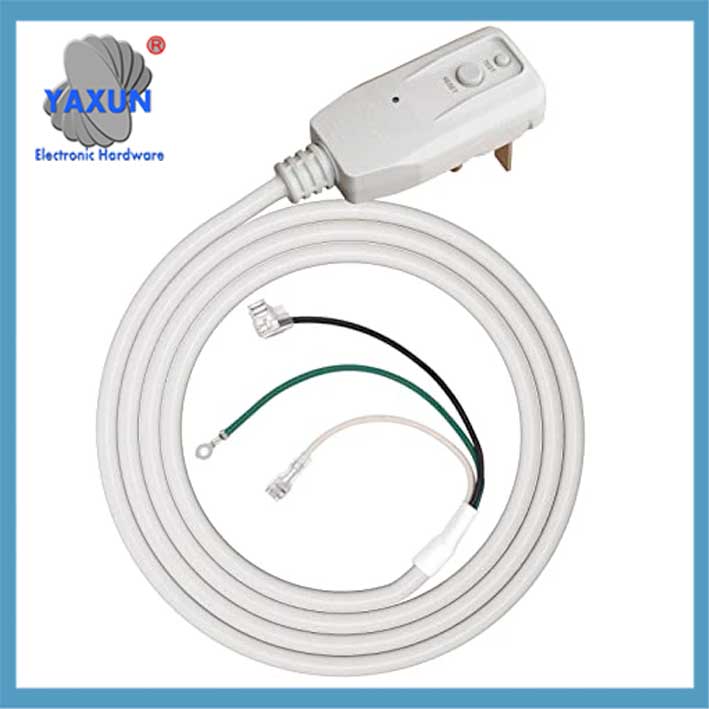
Air Conditioning Extension Cable AC240V 10Amp 2400W 60Hz NEMA5-15P Leakage Current Detection
Then we have to ask, does it have to be segmented?
My point is, it should be analyzed on a case-by-case basis.
When designing the CATIA wire harness layout, the wire harness layout in the vibration area and the wire harness layout across relatively moving components are our key considerations. Zu diesem Zeitpunkt, the central guiding idea is: how to reduce or even eliminate the impact of movement on the wiring harness connection performance as much as possible.
There are a few points to pay attention to:
1. Eliminate the stress concentration problem on the wiring harness terminals as much as possible to avoid subjecting the connecting terminals to additional pulling force.
The main methods to eliminate stress concentration in wire harnesses are:
A. The wires at the end of the plug-in must not be wrapped loosely
The wires at the end of the plug-in should not be wrapped too close (Notiz: the length of L generally refers to the distance between the farthest terminals of the connected plug-in)
The wiring harness at the end of the plug-in needs to be effectively fixed within 100mm.
2. Analyze the relative movement distance and reserve the length of the wiring harness. If the wire harness is segmented, the Inline plug-in must be effectively fixed (rotation is not possible)